Industrial processes are constantly optimised by engineering and technical service staff using a range of sensor inputs but often without context. This project installed utility metering, sub-metering and additional sensors to create normalised figures for industrial energy KPIs.
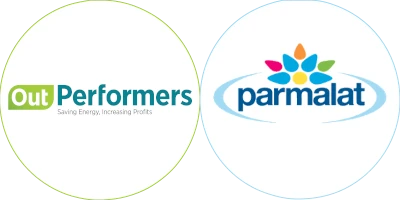
Location: Australia
Industry: Milk Processing Factory
Project Funding: $180k
Project Website: Lactalis Parmalat
Assets: 8 processing facilities
Employees: 2,250
Key Outcomes
- Up to 30% less energy consumed
- Up to 50% less maximum demand
- Up to 15% improved equipment lifecycle
- Monitoring 5 sites from a web-based portal
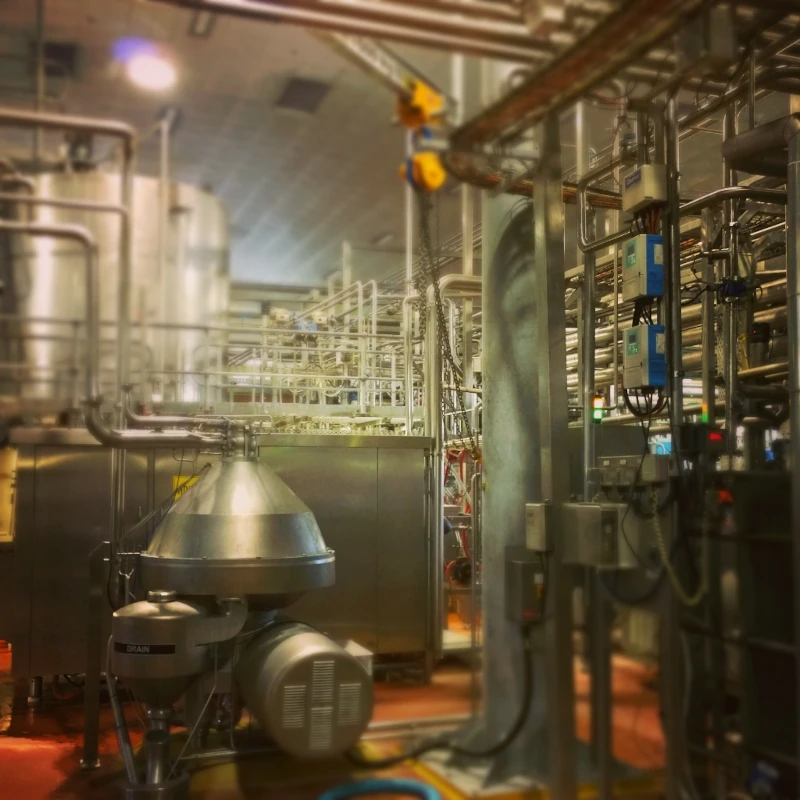
Scope
Out Performers engaged Buildings Evolved to design and procure services for the installation of metering, monitoring and other sensors to the Lactalis Parmalat manufacturing plant located at Lidombe in Sydney, Australia.
Gas Metering
Due to the scale of consumption and demand, it was decided to add pulse logging to the Jemena gas Volume Boundary Meter (VBM).
Jemena VBM - added a client interface panel and connection to SCADA
Air Compressors
Timing of startup of air compressors as well as the efficiency of compressed air generated was a focus of monitoring. Air volume sensors and electricity consumption metrics were used together to provide an efficiency rating to monitor over time.
Flow meters and electricity meters connected to Atlas Copco compressors.
Glycol Chillers
Milk processing plants along with many industrial processes require glycol chillers to provide subzero temperatures through reticulated pipework. Being a large energy consumer on site, it was important to understand the operational schedules as well use the data for predictive maintenance. Sensor data from the glycol chillers was combined with electricity consumption data to provide a normalised efficiency metrics for industrial energy KPIs.
Glycol chiller heat exchange plate.
Production Line Equipment
Selected production line equipment was monitored using the following sensors:
- Compressed air flow rates.
- Chilled water temperature.
- Glycol temperature.
- Steam flow rate.
- Number bottles produced.
These metrics were then compared with input electricity and gas consumption data to provide normalised efficiency figures and key industrial energy KPIs for the production line.
Controls panel housing electricity meters for production line equipment.
Sub-meters
Throughout, Socomec electricity meters were used - the preferred vendor of Lacalis, the French parent company of Parmalat. Using a standard data bus, they were terminated onto Moxa modbus gateways that ultimately connected the meters to the SCADA local area network.
Array of Socomec submeters on a test panel prior to installation on site.
Wireless Bridge
The boiler house is located away from the production facility and due to the period constructed, included no network cabling. Cost of installing cabling (given heights, distances and interruption to the loading docks) was priced and was expensive. Alternatives were sought. We added an industrial Moxa wireless bridge and antenna system to the main building and the boiler house, delivering vortex flow sensor and boiler gas consumption data to the SCADA.
Moxa wireless bridge installed in the boiler house.
SCADA Integration
The various flow, temperature, gas and electrical meters were connected to the site Citect SCADA (now AVEVA Plant SCADA, now Schneider Citect). The data was used to create normalised figures across the production lines:
Graph of blow moulder air compressor vs compressed air power.
Crosstab of blow moulder air compressor vs compressed air power.