Industrial processes are constantly optimised by engineering and technical service staff using a range of sensor inputs but often without context. This project installed utility metering, sub-metering and additional sensors to create normalised figures for energy KPIs.
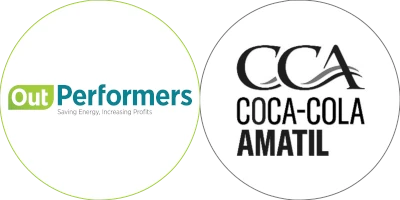
Location: Australia
Industry: Beverage Manufacturer
Project Funding: $400k
Project Website: Coca-Cola Europacific Partners
Key Outcomes
- Energy cost normalisation introduced
- Plant & equipment efficiency monitored
- Energy KPIs for Efficiency Opportunities now identifiable
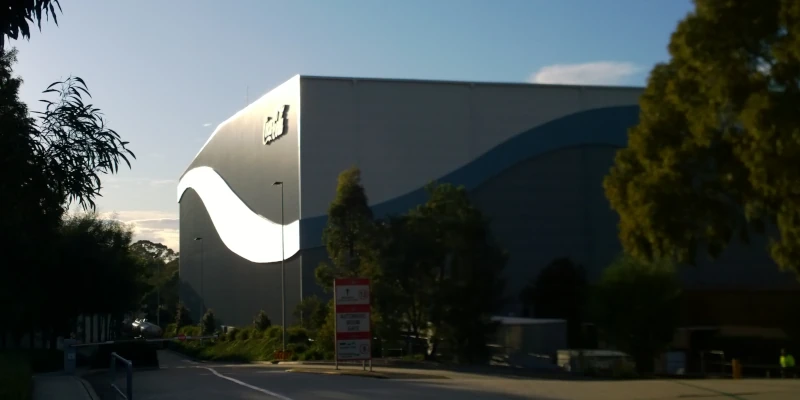
Scope
Out Performers engaged Buildings Evolved to design and procure services for the installation of metering, monitoring and other sensors to the Coca-Cola manufacturing plant located at Northmead in Sydney, Australia.
Project team electricians installing equipment in CCEP Northmead
Gas Metering
Due to the scale of consumption and demand, it was decided to add pulse logging to the Jemena gas VBM, the Sydney Water meter and the Origin/Acumen electricity utility meter on the incoming HV lines.
Jemena VBM - added a client interface panel and connection to SCADA
Water Metering
With overall energy consumption and demand now being logged in real-time, the plant operators could understand ways and means to flatten out electrical demand through scheduling of plant operations.
Sydney Water with pulse read head installed
Electricity Monitoring
Arrangements were made with the meter data agent (Acumen) to supply a real-time modbus connection to the EDMI meter.
The EDMI MK10E metering the HV supply, upgraded to support Modbus
Submetering + Sensors = Metrics
The project sought far more detail than purely bulk energy supply. Network based sub-meters from Northern Designs were installed on key energy consuming equipment. Sensors, if lacking, were added to measure the output of the plant and equipment These metrics were intended to be integrated into the on-premise SCADA system so that normalised metrics could be created; for example:
- compressed air energy cost
- cost per production run per machine
This data is stored and compared over time to track loss of efficiency in the production line, or for preventative maintenance purposes.
ND submeter on L2 Shrink Wrapper (reading 25.1A)
Plant & Equipment Covered
The submetering and additional output metric sensors covered to enable energy KPIs to be tracked from key energy consuming equipment:
- air compressors;
- blow moulders;
- water treatment plant;
- shrink wrappers;
- can line airveyor;
- sugar dissolver; and
- blow-fill cooling towers.
Reference Design
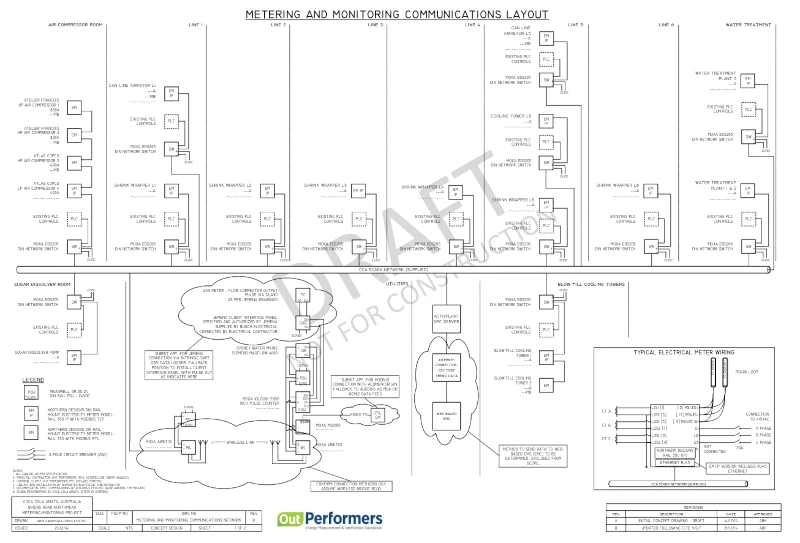